In a Manual System
There are different levels of traceability. The basic requirement is to trace a sterilized item back to its sterilization batch, usually done with a batch sticker on the item. However, this doesn’t automatically provide traceability from the batch to the item. To find all items from a batch, manual checking is necessary. This becomes more complex when an item is used on a patient. After use, the sticker is moved to the patient’s notes, allowing identification of the batch, but not the specific item.
Full Scope of Traceability
Item to batch, however, is just one minor aspect of traceability. The following diagram shows the potential scope of traceability for an item. The diagram then provides examples of the type of question you can answer if you have this information and when it is likely that you would ask such a question. There are many more questions that can be asked and answered but this will give you a good starting point to understanding the potential of LTrace.
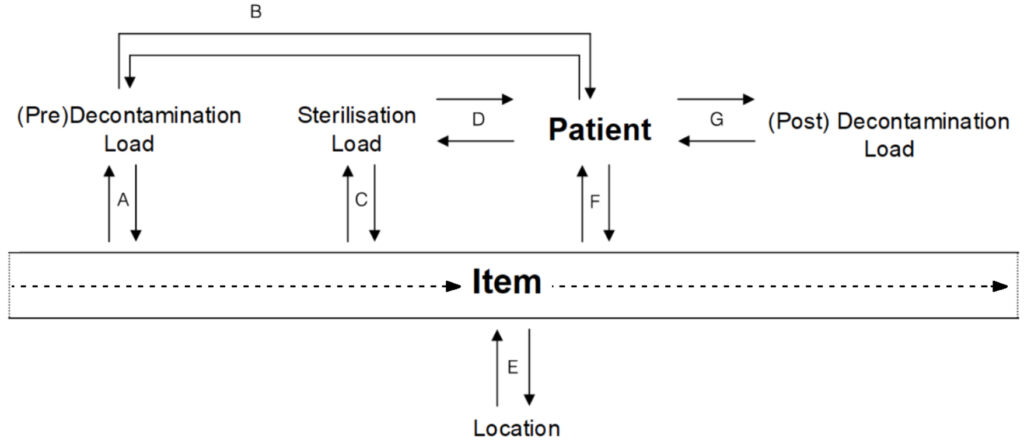
A.
Pre-Decontamination Load to Item:
- Which items were washed in this load?
Item to Pre-Decontamination Load:
- When was this item last washed?
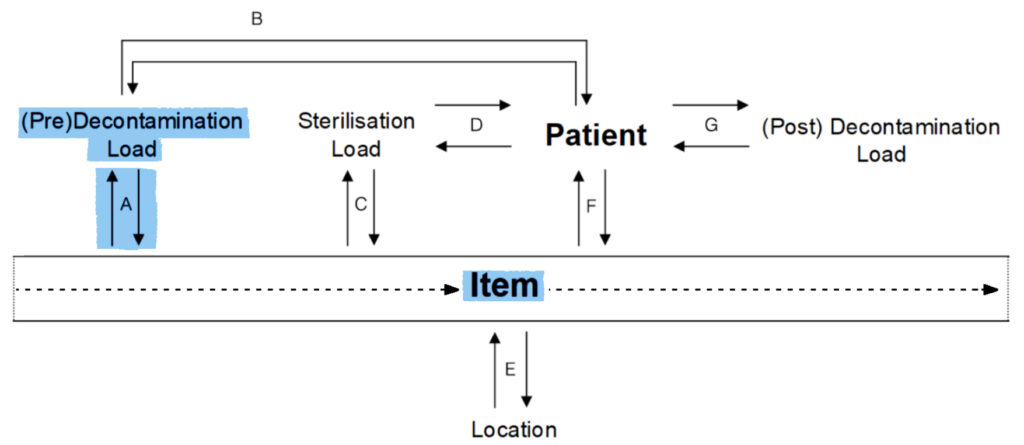
B.
Pre-Decontamination Load to Patient:
- Which items were washed in this load?
Patient to Pre-Decontamination Load:
- This patient used items from which loads?
- Is there a common load for these patients?
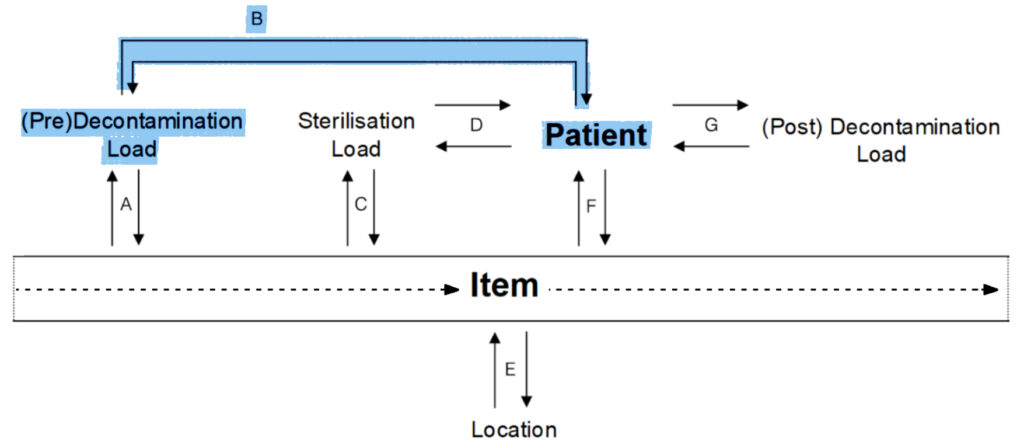
C.
Sterilisation Load to Item:
- Which items were sterilised in this load?
Item to Sterilisation Load:
- When was this item sterilised?
How often has this item been sterilised? - In which batch was this item last sterilised? (This last question is the only question a manual tracking system can answer quickly)
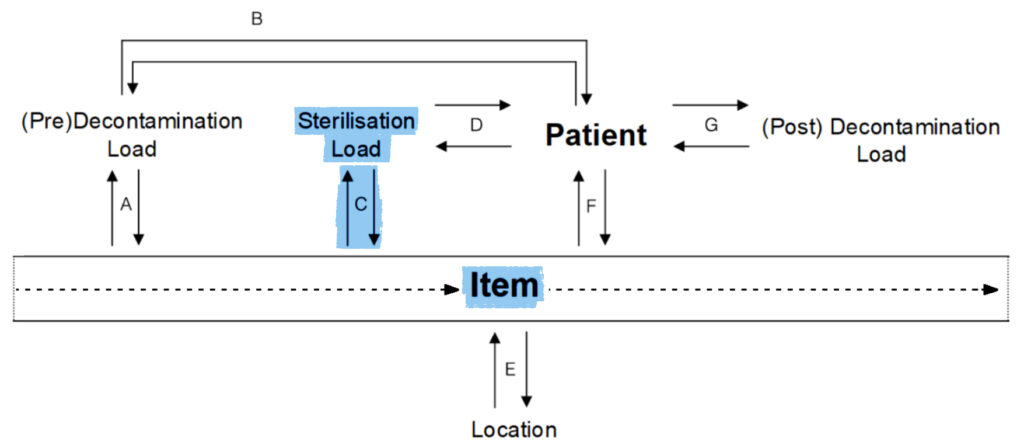
D.
Sterilisation Load to Patient:
- Which patients used items from this load?
Patient to Sterilisation Load:
- This patient used items from which loads?
- Is there a common load for these patients?
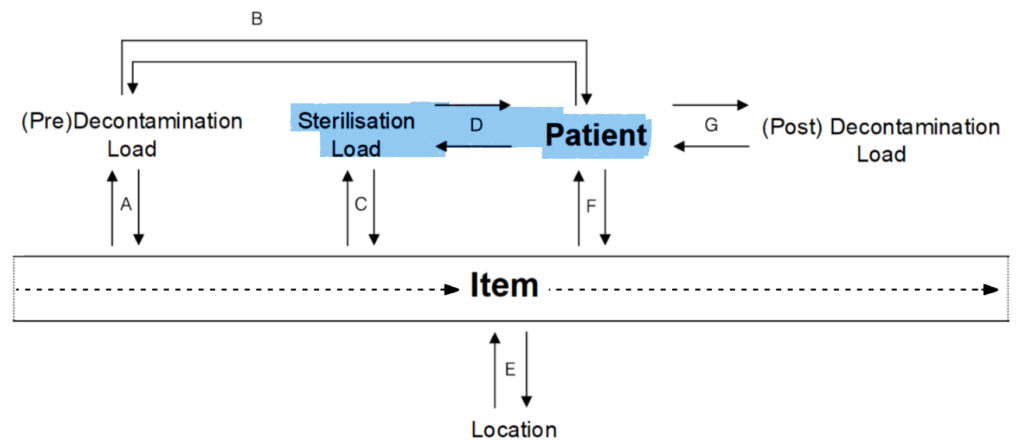
E.
Item to Location:
- Where is this item?
Location to Item:
- What items are at this location?
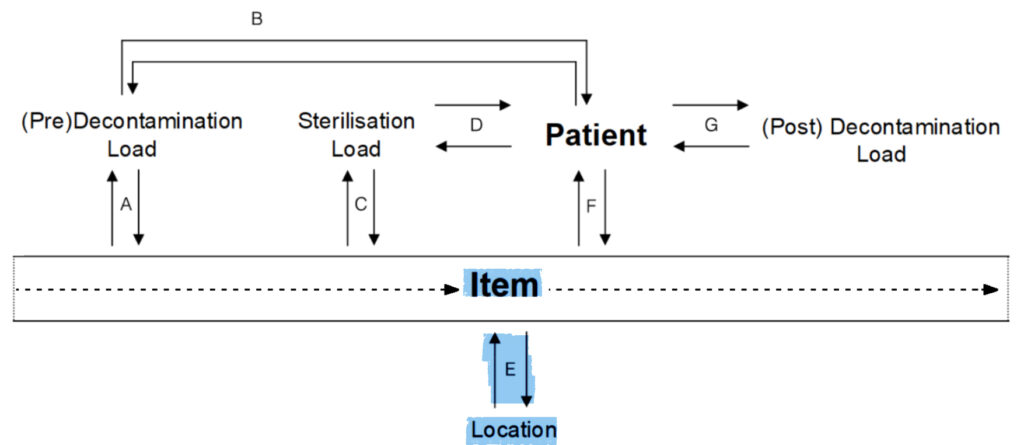
F.
Item to Patient:
- Which patients used this item?
Patient to Item:
- Which items were used by this patient?
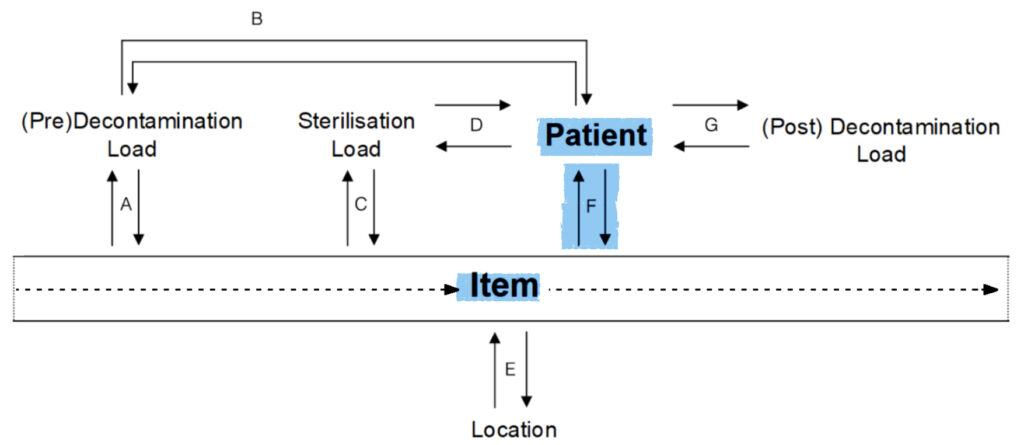
G.
Pre-Decontamination Load to Patient:
- This load contained items from which patients?
Patient to Pre-Decontamination Load:
- In which loads did this patient have items washed in?
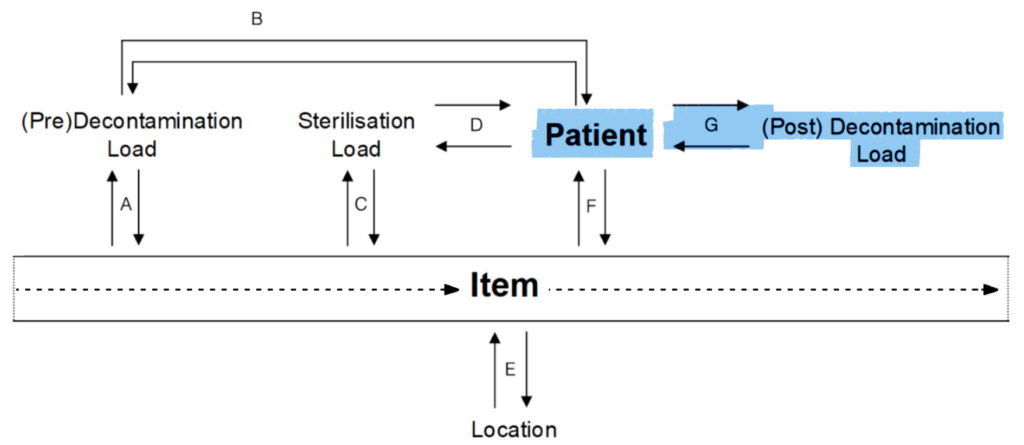
Then there are questions that are answered by combinations of the above such as:
- Where are the items that were sterilized in this load? (BP: Sterilisation to item to location)
- Who else used items sterilized in the same loads as those items used on this patient? (FABE: Patient to the item to sterilization to the item to the patient)
Centralizing information makes answering questions and managing inquiries easier and quicker.
- How many loads happened each day?
- How many items are processed during each hour of the day?
- What is the average number of items per load?
- How many items are rejected?
- How many items get returned unused?
- What items are in short supply?
CJD
CJD tracking requires the ability to track an item from patient to patient. To achieve this the item must be uniquely identified within L-Trace. This allows tracking from the patient to the specific item back to the patient (E + F) and is shown as G and H in the diagram.
Pre and post decontamination
A manual label system focuses only on the sterilisation batch for the patient. LTrace extends this to the decontamination batch before sterilisation (pre-decontamination) through to the decontamination batch after its usage (post-decontamination).
- Pre-batching is when the item has been decontaminated before its usage.
- Batching is when the item has been sterilised before its usage.
- Post-batching is when the item has been decontaminated after its usage.
Where this concept becomes more complex is when the focus is placed on a decontamination batch. In this case it is useful consider what happens to various types of items.