Unique vs Non-Unique Items
Unique items allow staff to identify specific items or exact sets, whereas non-unique items only help identify the type. The advantage of unique items lies in the ability to track which sets have been used, who used them before, and who will use them next, providing crucial information for CJD traceability.
Unique Items
A unique item remains traceable throughout its usage cycles, with the previous label linked to the next label. In practical terms, the decontamination batch serves as the post-batch for the first label and the pre-batch for the next label. Each batch is associated with two labels: one that entered dirty and another that emerged clean.
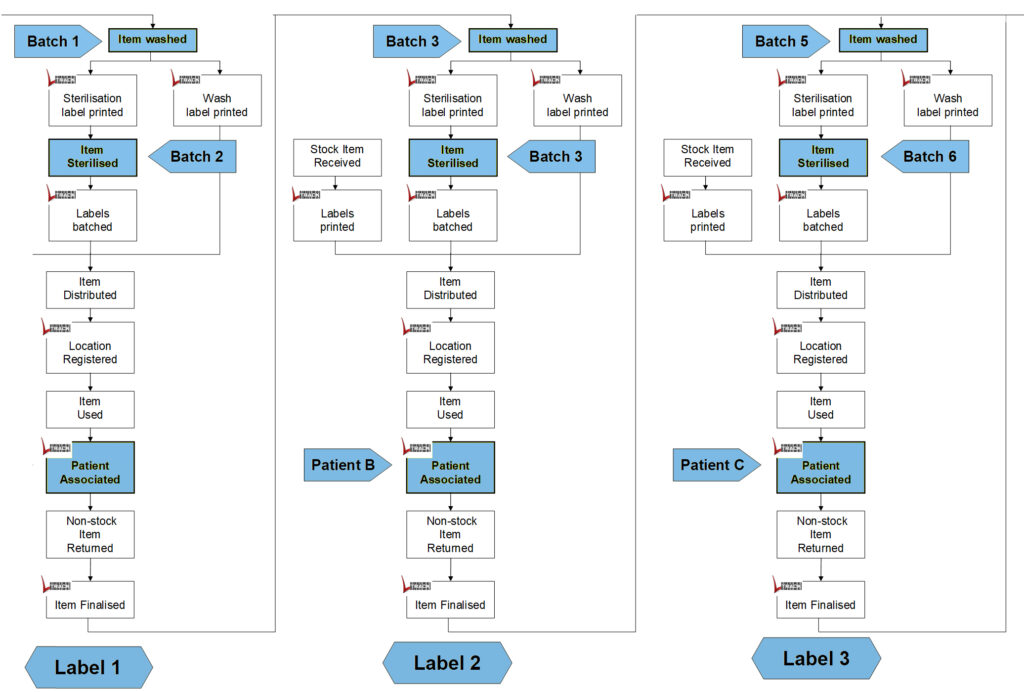
Examining the table reveals that both labels 1 and 2 were part of batch 3, while labels 2 and 3 were associated with batch 5. To simplify, consider that label 1 entered batch 3, and label 2 came out of batch 3. The actual creation or printing time of the label is irrelevant to this concept.
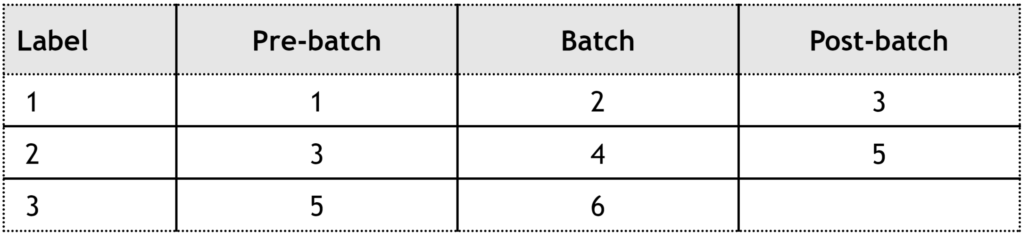
Non-unique items
In contrast, a non-unique item scanned back into a decontamination load will only terminate at the load. Decontaminated items in the load will have their pre-batch set, and there is potential for them to be later scanned back in with a post-decontamination batch set as well.
Does it matter?
The investigation into the source of an infection begins by retracing the steps to the decontamination load where the item was washed. The initial focus is on examining the pre-decontamination load. By reviewing all labels associated with the same pre-decontamination load, efforts are made to identify other patients who may have been infected or pinpoint items that require recall. Additionally, investigating labels with this batch as their post-decontamination load aids in locating the origin of the infection.
How is this achieved?
Achieving this level of traceability involves scanning labels back into the Central Sterile Services Department (CSSD) in the same decontamination load where they were cleaned. This is easily done when items have their own barcodes or when labels are removed from the wrapping and returned with the goods (e.g., on a “patient sheet”). The LTrace system also provides a list of recently used items. While this level of traceability exceeds current standards, it is highly recommended, especially as items are uniquely identified.
Other questions
This chapter primarily discusses tracking items, but it also emphasizes gathering additional information, such as:
- Equipment loads
- Equipment services
- Biotests
- Loan sets
- Fast track
- Additional items to be invoiced
- Locations
This expanded data allows the system to answer questions like:
- “How many loads have we done with each steriliser this month?”
- “How many breakdowns have we had?”
- “How reliable is the equipment?”
- “Which items are continually being fast-tracked?”
- “Which department uses the most of this item?”
- “Where are these items?”
With LTrace, obtaining quick answers to such questions becomes effortless, eliminating guesswork and the need for extensive paperwork. This information becomes valuable when recommending the need for more sets, as you can substantiate your recommendation with a comprehensive list of how often they’ve been fast-tracked over the past six months.